切削加工とは?種類や特徴から製作できる代表的な部品例までを徹底解説
- 加工技術
切削加工(せっさくかこう)は、金属や樹脂などの材料を刃物で削って目的の形状に仕上げる基本的な加工技術です。試作から量産まで広く利用されているため、製造工程の基礎として理解しておくと役立ちます。
本記事では、切削加工の定義や代表的な種類や加工で使用される材料やメリット・デメリットまでをわかりやすく解説します。
切削加工とは?
切削加工とは、工作物(素材)に対して工具を用いて不要な部分を削り取り、目的の形状に仕上げる加工方法です。主に金属材料を対象に、精密な寸法や滑らかな表面を得るために使われていて、鉛筆削りやかんなを使った作業も切削加工の一例です。英語では「cutting process」と呼ばれ、製造業では非常に一般的な加工技術です。
切削加工は、工作物を回転させるか固定するかによって大別されます。
旋削 | 工作物を回転させ、固定された工具で削る(例:旋盤加工) |
転削 | 工具を回転させ、固定された工作物を削る(例:フライス加工) |
切削加工の代表的な種類
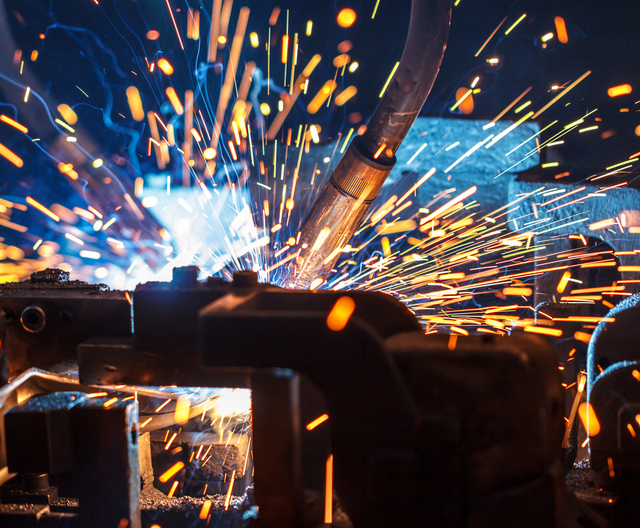
ここでは、切削加工の代表的な種類を3つ紹介します。
- 旋盤加工(旋削)
- フライス加工(ミーリング)
- 穴あけ加工(ボール盤・ドリル加工)
1. 旋盤加工(旋削)
旋盤加工は、工作物自体を回転させ、固定された刃物で表面を削る方法です。主に円筒形の部品に対して有効で、外周の切削や、内径加工(穴あけ)、ねじ切り加工などに用いられます。
代表的な旋盤には以下があります。
汎用旋盤 | NC旋盤 | CNC旋盤 |
![]() |
![]() |
![]() |
手動操作で加工する機械 | 数値制御による自動加工が可能 | 複雑な形状や高精度加工に対応する高度な制御装置付き |
2. フライス加工(ミーリング)
フライス加工は、固定した工作物に対して回転する工具(フライス)で切削する加工方法です。使用される工具は、正面フライス、エンドミルなどが一般的で、面削り、段差加工、溝加工など多様な形状に対応できます。
代表的なフライス加工には以下があります。
汎用フライス盤 | NCフライス盤 | マシニングセンタ(MC) |
![]() |
![]() |
![]() |
手動で加工操作 | 自動化された制御で加工 | ATC(自動工具交換機)を備え、3軸〜5軸方向からの加工に対応 |
3. 穴あけ加工(ボール盤・ドリル加工)
穴あけ加工は、ドリルやボール盤を用いて素材に穴をあける加工方法です。多様な形状の部品において不可欠な工程であり、切削加工の中でも非常に汎用性の高い手法です。
代表的な穴あけには以下があります。
穴あけ | リーマ加工 | 中ぐり加工 | ネジ切り加工 |
![]() |
![]() |
![]() |
![]() |
工作物を貫通させる | 穴径の精度を高める | 既存の穴を拡張する | タップを用いてねじ山を形成する |
切削加工の特徴【メリット】
切削加工には以下のようなメリットがあります。
- 低コストで工期が短い
- 高精度・高品質な仕上がり
- 少量多品種生産に適している
- 幅広い材料に適用できる
低コストで工期が短い
切削加工は、金型が不要で、工具と工作物さえあれば加工ができるため初期コストが抑えられます。また、加工時間が短く、急な試作や少量生産でも迅速な対応が可能です。
開発期間の短縮やスピーディな市場投入を行いたい場合に向いています。
高精度・高品質な仕上がり
切削加工では、ミクロン単位の精度で加工することが可能です。特にCADの設計データを利用することで、工作機械に読み込む数値データ(NCプログラム)を効率的に生成できます。
データを用いてCNC旋盤やマシニングセンタで精密な部品が製造できるため、航空機部品や医療機器など、高精度な部品が必要な分野に活用できます。
少量多品種生産に適している
金型に依存せず、設計変更にも柔軟に対応できるため、試作品や多品種小ロットの製造に最適です。短い期間で試行を繰り返すことも可能なため、品質向上や機能改善もスムーズに行えます。
幅広い材料に適用できる
切削加工は、鉄やアルミなどの金属だけでなく、樹脂、木材、セラミックなどさまざまな素材に対応可能です。幅広い製品設計や異素材の組み合わせによる開発にも応用できます。
切削加工の注意点【デメリット】
切削加工の課題や注意点について理解しておきましょう。
- 切り屑の処理コストがかかる
- 大量生産はコスト高になりがち
- 摩擦熱の対策が必要になる
切り屑の処理コストがかかる
切削加工では、削った分の材料の切り屑が廃棄されます。工作機械や工作物に挟まり悪影響になるだけでなく、材料の歩留まりが悪くなりリサイクルや処分の手間もかかります。
大量生産はコスト高になりがち
切削加工は柔軟性に優れていますが、金型を用いるプレス加工や鋳造加工と比べ、1個あたりの加工時間や手間がかかるため、大量生産には不向きです。製造工数などによりコスト面で劣ることがあります。
摩擦熱の対策が必要になる
切削加工は工具と工作物が高速で接触するため、摩擦熱が発生しやすく、加工精度や工具寿命に影響を与えます。特に精密加工では、切削油(クーラント)による冷却や、適切な工具の選定などによる摩擦熱への対策が重要です。
材質別の切削加工方法

切削加工に用いられる素材の物性は多岐にわたるため、適切な切削加工方法を選ぶことが重要です。ここでは、一般的な材質に用いられる加工技術や注意点を紹介します。
- ステンレスの加工
- アルミニウムの加工
- カーボンの加工
- 銅・真鍮の加工
ステンレスの加工
ステンレス鋼は、医療機器や厨房設備、建築構造材など幅広い分野で活用されています。
ステンレスの主な特性 | |
耐食性 | SUS304は塩水環境でも錆びにくい |
高強度 | 引張強さが500~750MPa |
耐熱性 | 800℃以上でも形状保持が可能 |
一方、ステンレスは難削材として扱われることもあります。
- 熱伝導率が低く、切削時に工具が過熱しやすい
- 加工硬化が起こりやすく、切削が進むほど硬くなる。(特にオーステナイト系ステンレス(SUS304、SUS316)で顕著)
加工硬化が起きると、加工中に変形した部分が急激に硬化して工具の負荷が増大します。そこで、ステンレスを加工する際は以下の対策を取ることがあります。
- 超硬合金工具やセラミック工具の使用
- 冷却性に優れた水溶性切削油の活用
- 一度に切り込む深さを最適化し、加熱時間を抑える
【関連記事】
ステンレスとは?特徴・種類・錆びにくい理由を詳しく解説
アルミニウムの加工
アルミニウムは、軽量かつ加工性に優れているため、航空機部品や高級スポーツカーのフレームなど、軽量化を目的とする製品に広く使われています。
アルミの主な特性 |
比重が2.7と小さく、鉄の約1/3の軽さ |
熱伝導率が高く、放熱性に優れる |
延性が高く、複雑な形状の加工に向いている |
一方で、アルミの切削では、加工中にアルミの一部が工具に付着して刃先を覆う構成刃先が問題となることがあります。これは仕上げ面の粗さや寸法精度の悪化を引き起こすため、以下などの対策が有効です。
- エアブローや切削油を用いた冷却・潤滑
- コーティング工具の使用
- 高回転・高送りで短時間の切削を心がける
カーボンの加工
カーボン素材は、航空機の翼部材や高級自転車のフレームなどに使用されます。特にCFRPの引張強さは2,000MPa超と、同重量の鋼材より数倍の強度があります。
カーボンの主な特性 |
軽量 |
高強度。特にCFRP(炭素繊維強化プラスチック) |
しかし、カーボンの切削加工には以下の課題があります。
- 粉塵が機械の可動部に侵入し、故障リスクが高まる
- 刃物の摩耗が激しく、工具寿命が短くなる
- 加工中に発生する微細粉塵が人体に悪影響を及ぼす
これらのリスクを抑えるため、カーボンを加工する際は以下の対策を取ることがあります。
- 粉塵吸引装置や集塵機の併用
- 高硬度コーティング工具(PCDやCBN)を使用する
- 加工者には防塵マスクや防護眼鏡の着用を徹底する
銅・真鍮の加工
銅や真鍮は、5円玉や電子部品、装飾品、金管楽器(トランペット等)などに用いられます。
真鍮の主な特性 |
電気伝導性が良い |
加工しやすく、バリが出にくい |
熱伝導性が高く、放熱部品に向いている |
錆びにくく、美しい外観を保ちやすい |
しかし、銅系材料は溶解温度が低く、切削加工時に発生する切り屑が工具に付着して、仕上がり精度が低下しやすいという課題があります。これらのリスクを抑えるため、銅や真鍮を加工する際は以下の対策を取ることがあります。
- 油性クーラントを用いて切削点を潤滑・冷却する
- 材料をにあたるすくい角が大きい工具を使用する
切削加工で製作できる代表的な部品例
ここでは、切削加工の技術によって製作される代表的な部品や用途、加工内容について具体的に紹介します。
- 平面加工部品
- 多面加工部品
- 3軸加工部品
- 多軸加工部品
- 同時多軸加工部品
平面加工部品
平面加工部品は、1軸方向のみ単純な切削で加工できます。治具の段取りが単純で、短時間かつ低コストで製作できます。
ベースプレート | 取り付けや支持基盤となる部品 |
面取りブロック | 角部を斜めに削り、安全性や組付け性を高めた部品 |
多面加工部品
多面加工部品は、工作物の複数面に異なる方向から加工を行います。そのため、工作物の向きや位置を変更する段取りが必要で、複数回のセッティングが必要です。
段取りの精度が、完成品の寸法や公差にも影響を与えます。
ブラケット | 構造物の補強・支持に用いる複数の面に穴、溝、切り欠き加工のある部品 |
ハウジング | タップ穴加工などがあり、内部に部品を収めるケース状の部品 |
3軸加工部品
3軸加工部品は、X・Y・Zの3軸方向を同時制御して加工する部品です。ボールエンドミルなどの工具を使用し、CAMを用いて加工パスを生成して高精度に仕上げます。
- 金型のコア・キャビティ
- 自由曲面のカバー部品
- 人工関節
多軸加工部品
多軸加工部品は、5軸加工機などで自由曲面・ボス(突起)・肉抜き構造といった複雑な要素が組み合わさった形状を素材の向きを変更しながら一体的に加工します。高度な制御技術と段取りノウハウが不可欠です。
航空機用の構造部品 | リブ、フレームなど |
エンジンマニホールド | エンジンに空気を導入するための管 |
同時多軸加工部品
同時多軸加工では、素材と工具が複数軸で同時に動き、内部に入り組んだ曲面構造やねじれ形状を持つ形状について、精度と一体感を両立しながら一体成形できます。
ローターブレード | ヘリコプターなどのローターに付いている羽 |
インペラ | 補助循環用ポンプカテーテル |
切削加工の活用事例
ここからは、切削加工を用いた部品が使用される業界や製造現場での活用例について説明します。
- 自動車業界での事例
- 医療業界での事例
- 航空宇宙産業での事例
自動車業界での事例
自動車では、シフトノブなど外観や質感が求められる部品の造形に切削加工が多く用いられます。特にアルミホイールは、デザインの複雑さと強度の両立が必要であり、切削により立体感や精密な面取りを行います。
さらに、電気自動車(EV)技術の発展により、モーターの高効率化が求められています。走行用モーターに必要なモーターコアや製造用金型にも、切削加工技術が用いられています。
医療業界での事例
人工骨やプレート、金属製インプラントなどに切削加工が活用されています。たとえば、骨折部を固定する金属ボルトは、ステンレスやチタンなど生体適合性の高い素材を使用し、旋盤やねじ切り盤を用いてねじ山を高精度に形成します。
人体に直接埋め込まれる製品であり、極めて高い寸法精度と表面の滑らかさが求められます。
航空宇宙産業での事例
航空宇宙産業では、強度と軽さを両立するCFRP(炭素繊維強化プラスチック)を材料に、切削加工で飛行機の主翼・尾翼・胴体部材をはじめ人工衛星のアンテナ、太陽光パネルロケットのフェアリング(先端部)などを製造しています。
これらの部品は複雑な3次元形状と高精度を必要とし、加工時の振動・粉塵・工具摩耗への対策も不可欠です。
切削加工のまとめ
切削加工には旋盤加工やフライス加工、穴あけ加工があり、アルミニウムやステンレスなど幅広い材料を高精度かつ低コストに加工できる特徴があります。切り屑や摩擦熱の管理など課題への配慮は必要ですが、複雑な形状を作成したい場合の選択肢として有効です。
三和ニードルベアリングは、±0.0001mmレベルの高精度を具現化する超精密加工技術が強みです。高精度研削加工を軸に切削加工を組み合わせるなど、ニーズに合わせた加工を行います。
最小1個の試作品でも対応可能ですので、業界・用途・材質を問わず、お気軽にご相談ください。